Stories of Manufacturing #02
業界初の取り組み、
それ自体がチャレンジだったフレキシブルライン開発
次世代生産ライン誕生
福岡県にあるローム・アポロ株式会社広川工場で、半導体後工程の新ラインが稼働しています。2021年の4月に拡販用サンプル生産を開始。翌2022年からは、市販量産品としてディスクリート製品の生産を行っています。
「無人化・多品種生産ライン」というコンセプトを体現したクリーンルーム内には、コの字型に配置された3連の装置が整然と並び、その間をAGV(無人搬送車)が走行するコンパクトな設計。技術員は隣接したコントロールルームのモニターを通じて、すべてのラインの稼働状況を把握できるようになっています。
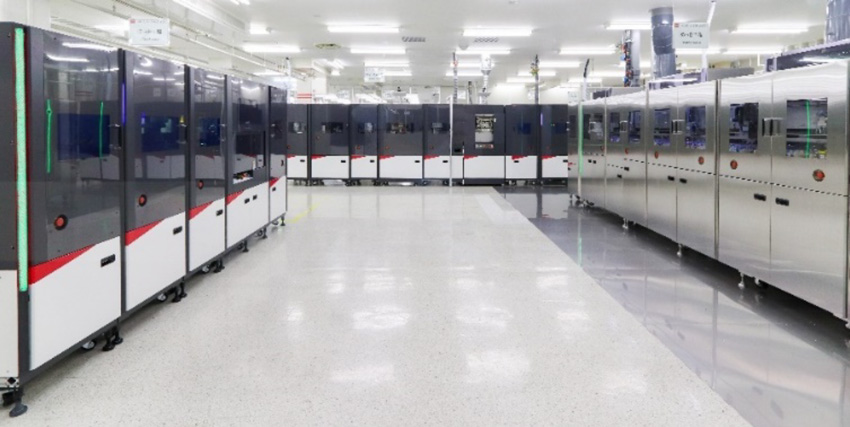
写真奥中央から First LINE【Die Bond→Gate Cut】
右に Middle LINE【Deflashing→Plating】
左に Final LINE 【Mark→Trim&Form】
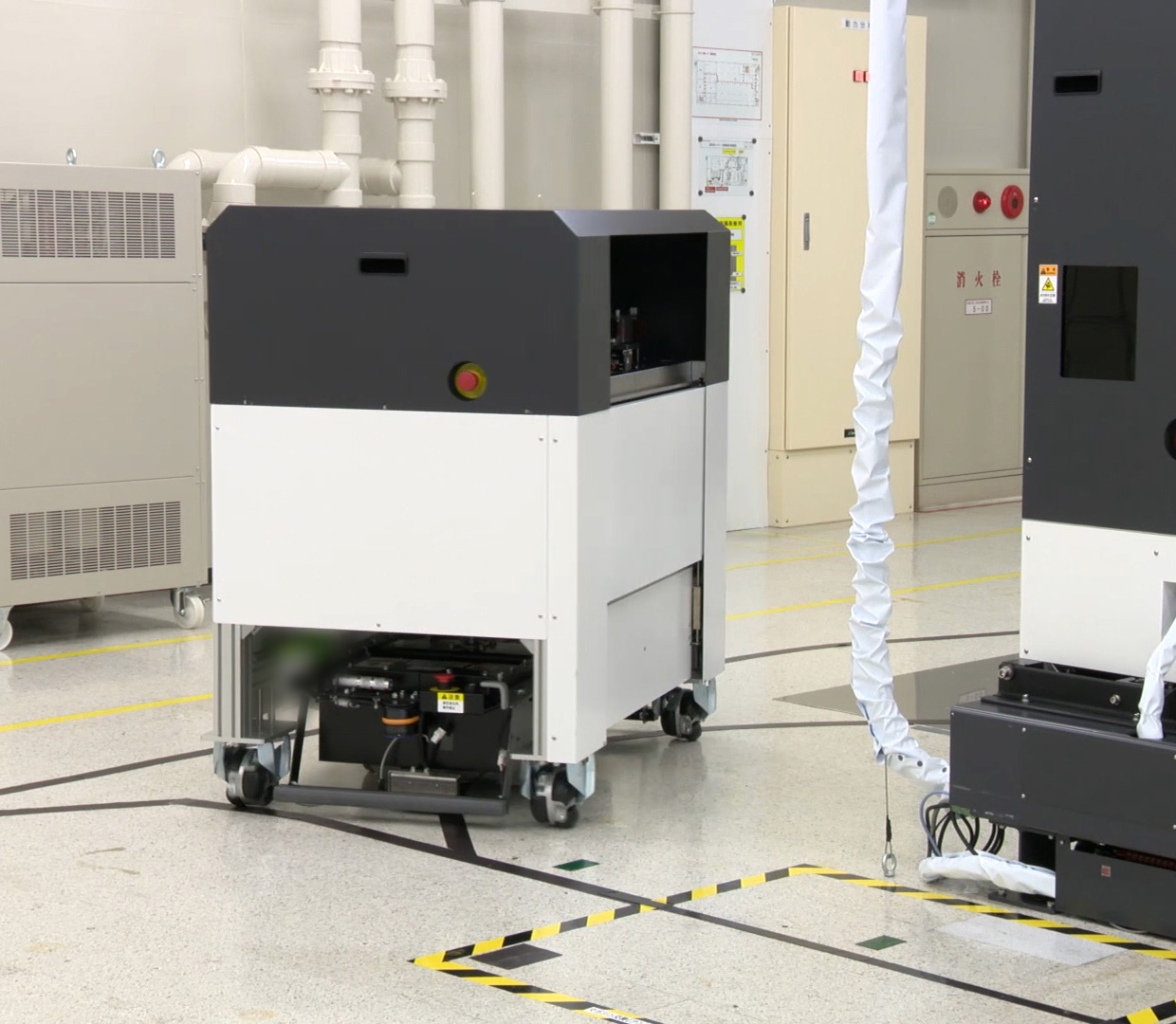
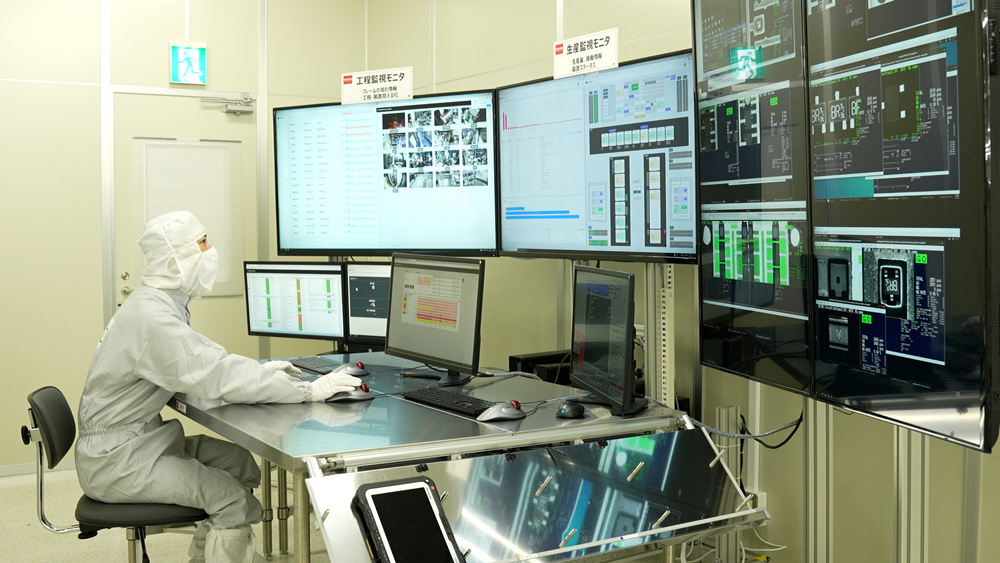
ロームの生産システム
ロームは1954年の創業以来、生産システムを自社で開発してきたという、半導体メーカーの中でも稀有な歴史を持つ企業です。1980年以降の後工程生産に於いては、三世代にわたる主力生産ラインの更新を推し進め、大量生産と品質向上、そして低コストの実現を図ってきました。
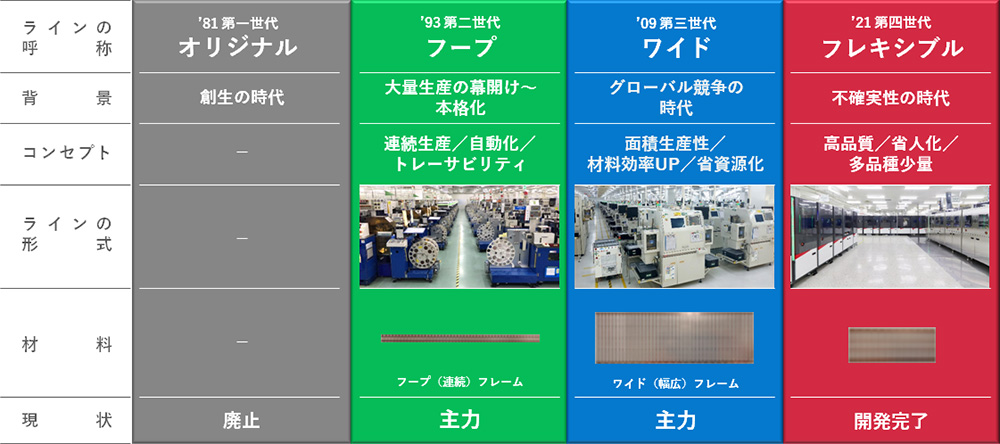
競合メーカーを交えた業界全体の競争原理はもとより、お客さまからのさまざまな要望をクリアすべく進化してきた生産システムの変遷について、長年にわたって生産システム構築に関わってきた「ものづくり革新部」三輪部長はこう語ります。
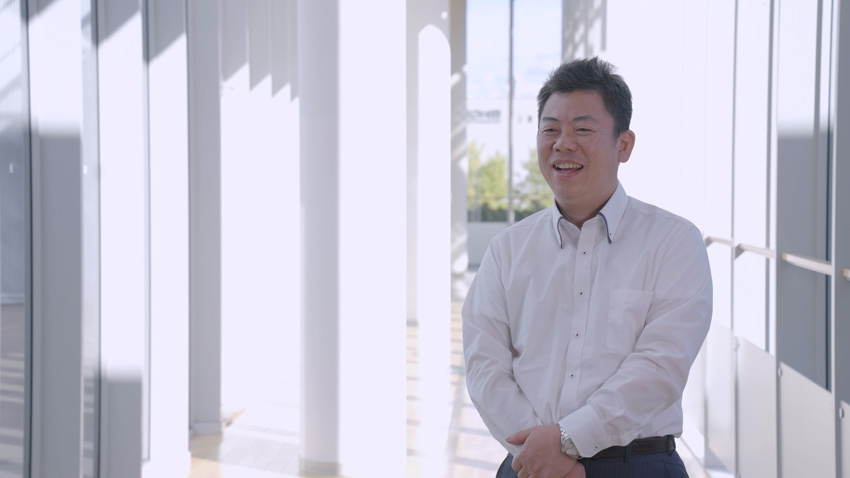
その当時、見学に訪れたあるメーカー工場で
「多品種大量生産」を実現している様子を目の当たりに・・・。
その時に感じた「ロームの弱点を突かれた思い」こそが、
フレキシブルライン開発の原点だったという。
ゼロディフェクトがミッション
三輪
「もうひとつ、生産性を高めるためにフレームを大きくすると、品質の面でどうしても一定以上に達しないというジレンマを抱えていたのも事実です。特に車載部品などを中心に、年々お客さま側からの品質要求がシビアになっていく時期でもありましたので、とにかく不良品の出ない生産システムを開発しようと。いわゆる<ゼロディフェクト>を目指したプロジェクトとしてスタートさせました。」
2018年にプロジェクトが本格的に稼働し始めて、量産検証にこぎつけるまで約1年半余り。当初からの大命題であった品質追求は勿論のこと、次世代の生産システムとしての要件を付加しながら検証していく道程は想像以上に険しいものだったと言います。
三輪
「これまでと全く逆の発想でモノを作るということですので、まず周りに理解者が居なかったというのが正直なところです。この理想の製造装置をどのように広めていくか、社内でも随分苦労しました。(苦笑)」
徹底した高品質設計
前述のワイドラインに代表される大量生産システムにおいては、最終工程での選別に加え、自工程完結型検査を導入することで品質レベルを担保しています。フレキシブルラインのコンセプト設計においては、あえて加工点から見直しを図るという大胆な方針が採られました。
現在、最前線でフレキシブルラインを担当する「ものづくり革新部」有賀統括課長に話を聞きました。
有賀
「われわれが打ち出したコンセプトは<加工点で品質を作り込む>ということです。工程のそれぞれの場所で品質を上げるために、設備面・材料面・そして作業面、そのすべてを洗い直すとこから始めました。
そのポイントは<5M1Eのバラつきの極小化>にあります。」
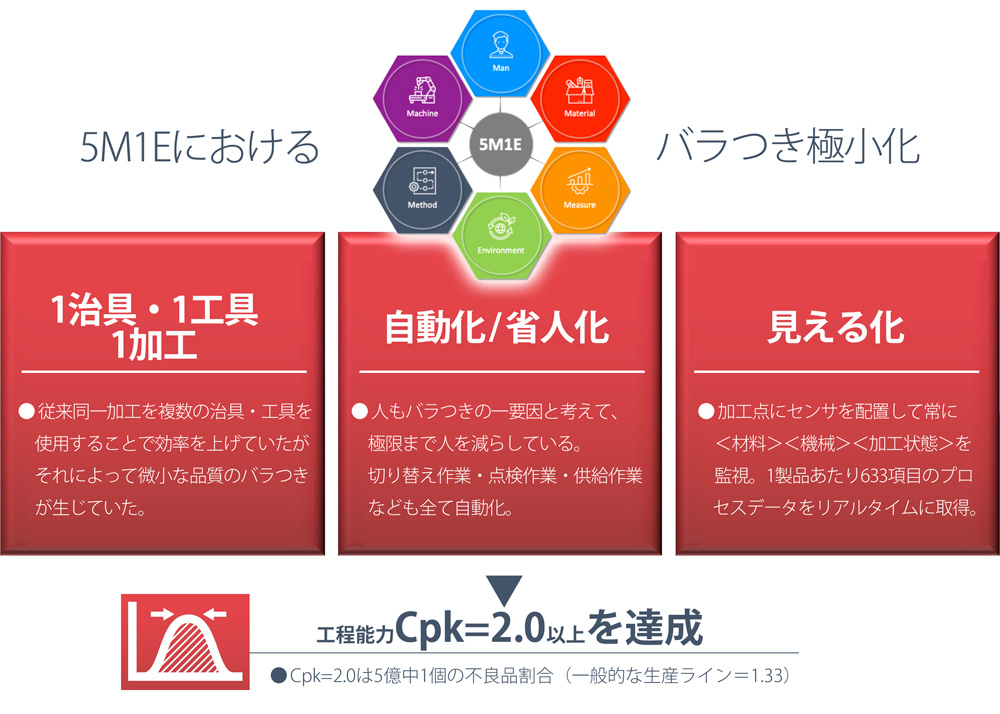
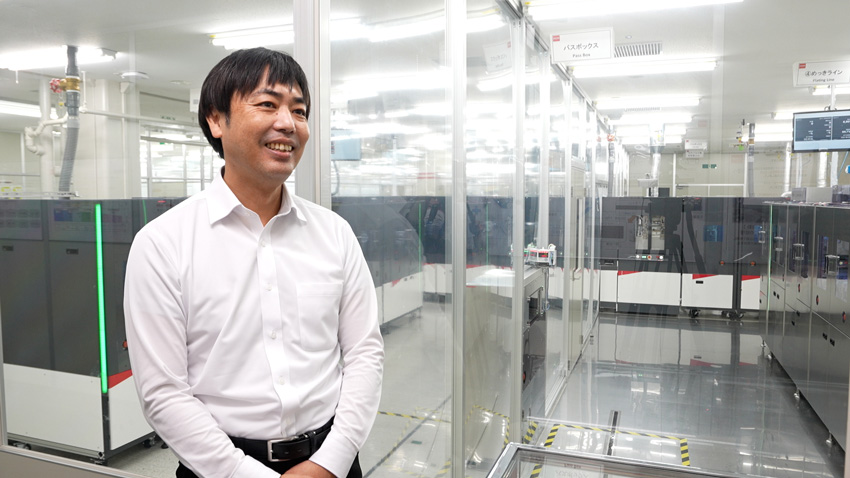
国内外からのお客さまをはじめ、エンジニアを目指す学生たちまでの来訪者対応として、クリーンルーム内の様子を観ることができるガラス張りの見学スペースを設置。
ここから見える最先端の設備に熱い眼差しが注がれる。
「半導体後工程製造ラインの開発、立ち上げ、量産移管までの一連の業務を担当しています。これまでに世界各国の工場に100台以上の装置を導入してきました。」
有賀
「これまで熟練作業員の経験やカンに頼っていた部分も多くあったのですが、数値化することで品質はもとより、さまざまなトラブルを未然に防ぐという点でも大きな効果が期待できます。 また、万が一お客さまからの問い合わせが入った場合も、その原因をリアルタイムで、しかも製品1個単位まですべて逆上れる、徹底したトレーサビリティを実現しています。」
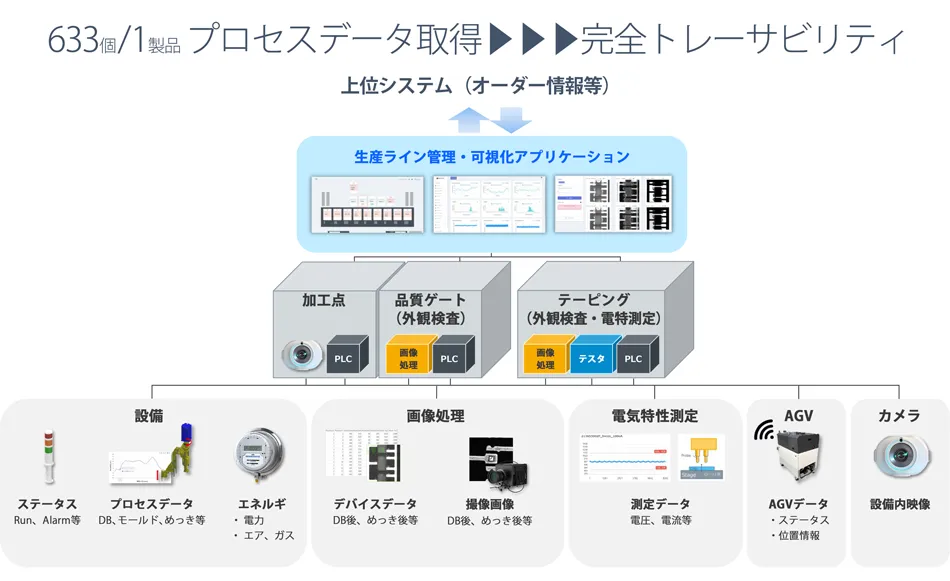
多品種少量生産
フル生産で450万個/月のポテンシャルを持つフレキシブルライン。現在は2品種のトランジスタを量産していますが(2022年現在)、近い将来10機種程度のラインアップに対応した市販量産を視野に入れているとのこと。
これは、前述の自動化による<切り替え>作業の簡素化によって可能になった、このラインならではの大きな特長です。その根幹には「大量生産一軸ではないものづくり」への挑戦という大きなテーマが内包されていると、ものづくり革新部の三輪部長は言います。
三輪
「大量生産/在庫設計が当たり前の業界の中で、初めて多品種少量生産に取り組んだ。それ自体がチャレンジだったと思います。大量受注品はワイドラインで、少量受注品はフレキシブルラインによる連続切り替え生産体制を構築することで、安定した供給体制を提供できると考えています。」
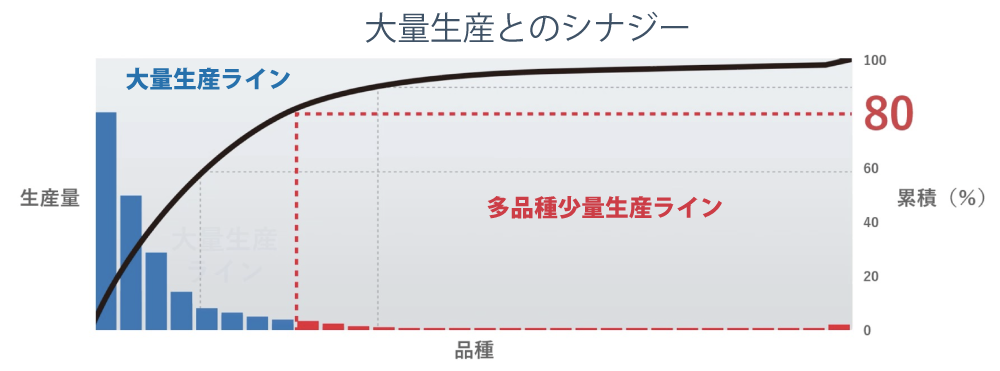

「必要なものを、必要なときに、必要なだけ。」 ロームのお客さまの中には、車載や産業機器分野のように少量だけど・長期間・安定して部品供給を望まれる方も数多くいらっしゃることを、強く意識しているという。
「フレキシブルラインの見学に来られた自動車メーカーのご担当者から<こんなことを考えついて、実現してくれるのはロームだけだ>との嬉しい言葉を頂くことができました。」
ONE ROHM そして技術継承
三輪
「ロームは一貫生産体制をとっていますので、部門を横断した摺合せ・意見交換が密にできる環境にあることが大事だったと思います。」
半導体業界の常識を覆すこのラインの開発には、多様な視点からの意見を集約することが欠かせませんでした。 また同時に、設計開発→試作評価→量産評価を繰り返しながら、それぞれの観点からブラッシュアップを続け完成度を高めていく、長期間に渡る協力体制が求められます。
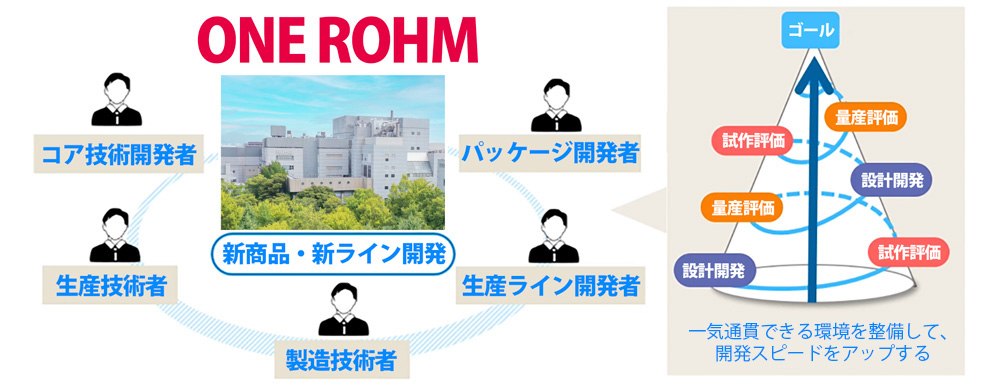
社内にそれぞれの部門のスペシャリストが在籍する、ロームならではの環境がこの困難なミッションを実現へと押し上げたと言えるでしょう。
三輪
「もうひとつのポイントは、我々が60年以上にわたって積み上げてきたノウハウや知見にあります。そういう意味では、このフレキシブルラインはロームの<技術継承>そのものと言えるでしょう。」
そう語る三輪氏自身も、開発現場では先頭に立って若いエンジニアと言葉を交わしながら、熱心に作業を見守っています。部門を超えた横のつながり、そして世代をこえて脈々と受け継がれていく知見とスピリッツ。このONE ROHMとしての価値を高め続けることで、「ものづくり」は一歩ずつ未来へと進んでいくのかもしれません。
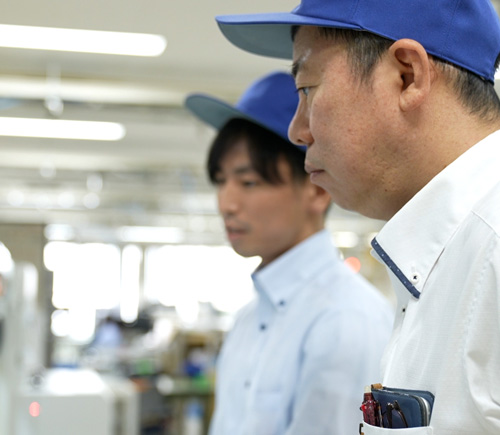
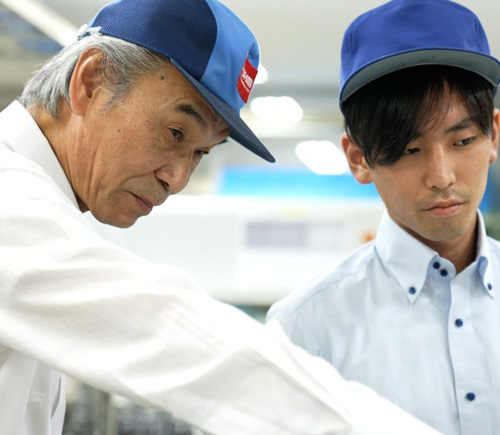
京都本社にある開発センターでは、国内外で使用されるさまざまな製造装置の設計・試作評価・量産評価などが毎日行われている。同時にこの場所は若いエンジニアが「ものづくり」を学ぶ現場でもある。
BCP対策 / 環境対策
フレキシブルラインが量産検証を開始した2020年。世界はcovid-19によるパンデミックの真只中にありました。世 界各国で半導体の生産・物流が滞るのを起点に、自動車・電子機器・家電に至るまでの多くの生産メーカーがその対策に追われたことは、まだ記憶に新しいことかと思います。
その後もエネルギー高騰・災害などの影響を強く受け、半導体不足は未だ解消されたとは言えず、日本国内でも生産拠点の見直しが進むなど、ものづくりを取り巻く環境は、刻一刻と変容しています。そういった時代背景も相まって、BCP対策に有効な生産システムとして、このフレキシブルラインに注目が集まっています。
増田
「このフレキシブルラインは自動化率が非常に高いので、全く同じライン設備を複数の拠点に敷設しておくことで、いつ・何時でも、同じ品質のものを、変わらず生産できる可能性を持ち併せています。
不透明な時代と言われる昨今の世界情勢の中で、安定してお客さまに製品をご提供するということを考えると、なくてはならない存在になるのではと考えています。」
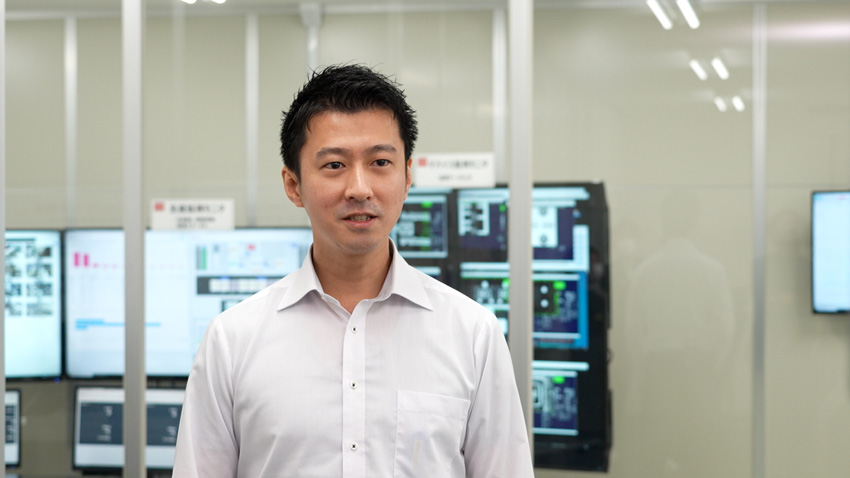
次世代ライン開発課 統括係長 増田 塁
自動化・省人化を徹底することによって、従来の生産ラインと比べた「人生産性」では約2倍。オペレーター作業時間は87%削減されるという驚きの数値が算出されている。
「上手く着地できるかどうか分からない、今回のプロジェクトのような案件に対して、自由にチャレンジできる環境を与えてくれる気風が、ロームにはあるんです。」
また、前述した「見える化」で収集されるデータを活用して、エネルギー使用量を常に可視化した状態で把握できるのも大きな特長のひとつです。地球環境保全が大きな課題となっている中で、電力由来のCO2排出量を抑制するとともに、省エネルギー化を推し進めたものづくりを目指しています。
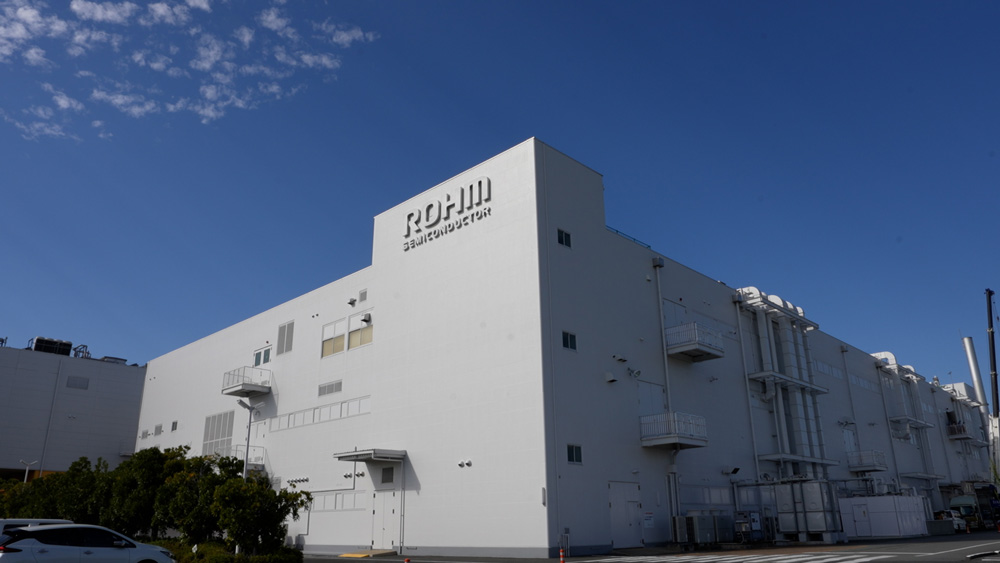
(福岡県八女郡広川町)
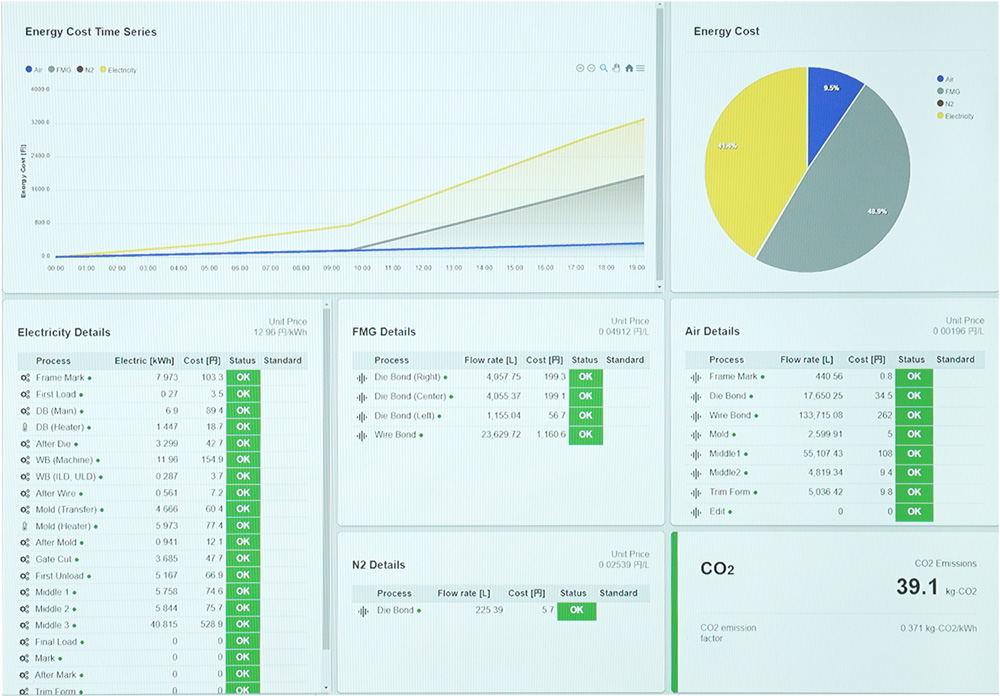
CO₂排出量に換算して見える化している
サステナブルな社会を目指して・・・
生産における環境性能が厳しく問われる時代。
サプライチェーンも含めた省エネ化・省資源化にローム全体で取り組んでいる。
新しいものづくりのプラットフォーム
増田
「現在、このラインで量産を行いながら、さまざまな技術検証を積み重ねている最中です。ここで得られた要素技術を、今後開発していく次世代型生産ラインに活かしていくことが当面のミッションとなります。」
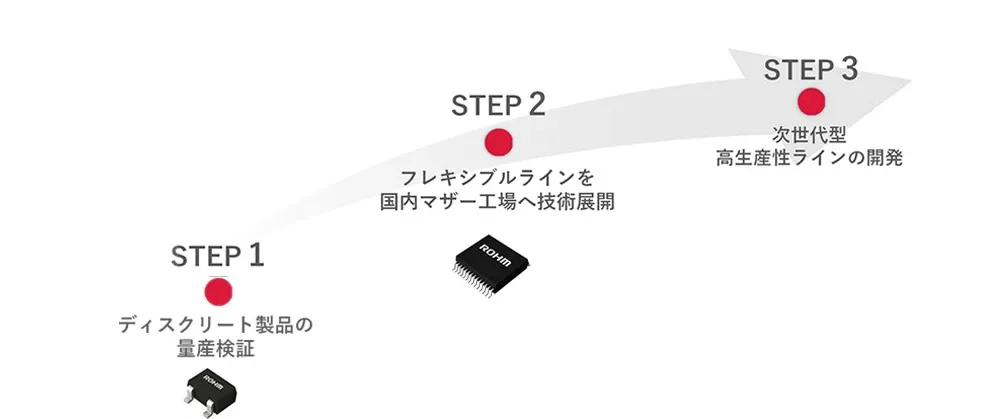
今後、広川工場での対応機種を拡大していきながら、その技術を還流させることで国内マザー工場へ展開。 数年先に見据えた無人化ワイドライン(大量生産ライン)の完成まで、どうやら一息つく状態にはないようです。 世界中のお客さまに信頼される新しいものづくりのプラットフォームへ・・・! その開発と進化はまだまだ続きます。
三輪
「90年代~2000年代にかけて、ロームではフープライン/ワイドラインと呼ぶラインを開発してきました。これらはその開発当時としては<品質第一・かつ大量生産で・ローコスト>を狙ったラインです。もちろん今現在もロームの主力生産ラインであることは間違いないのですが、加工実力や人生産性、リードタイムなどまだまだ改良の余地があると考えており、競合メーカーより1歩抜きん出たい・・・!といつも思っていたのが本音です。」