Stories of Manufacturing#04
ロームならではの「強み」を
「信頼」に変えるためにウエハ製造プロセス
アナログICの基幹工場
温暖な気候と豊富な水資源に恵まれ、江戸時代から続く繊維業をはじめ、楽器、バイクなど世界的なものづくり企業を育んできた土地として知られる浜松。
ローム浜松株式会社はこの地で1999年、ロームIC製品/LED製品の「前工程」を担う基幹工場として操業を開始しました。以来、デジタル市場の発展、市場のグローバル化、そして脱炭素・循環型社会へと変動する潮流の中、それぞれの時代のニーズに応える製品を市場に送り出してきました。
ロームが得意とするアナログICに特化した先進のデバイス・プロセス技術、生産設備を備え、ロームの生産するICの約70%以上を生産。8インチ、12インチの2つの生産ラインを有する工場からは、月産5万枚を超えるウエハが出荷されています。(※8インチ換算)
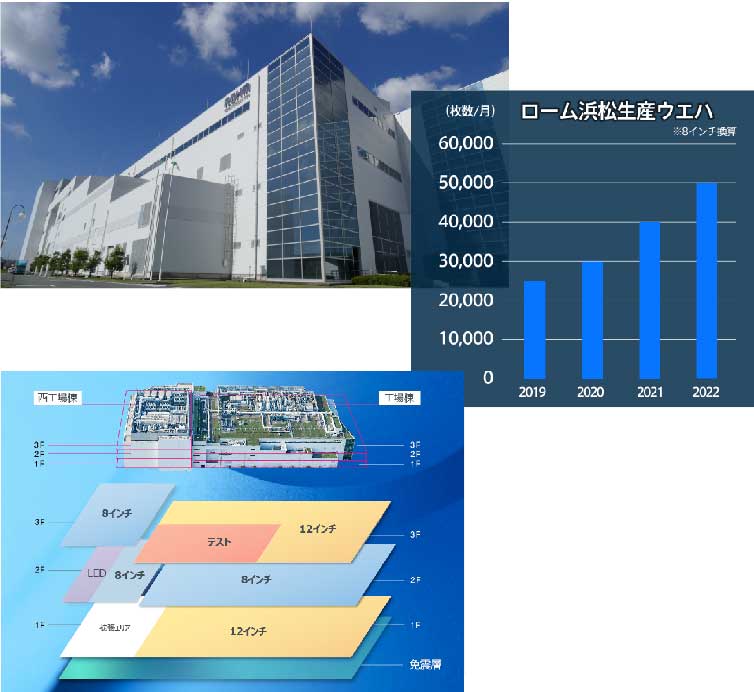
ローム浜松株式会社(静岡県浜松市)
約62,000㎡の敷地内に建つ2つの工場棟で構成。
半導体の工場としては世界で初めて免震構造を採用した。
工場全体の延べ面積約30,000㎡、クリーンルームの中央を貫く通路の長さは工場棟と西工場棟をあわせて約160mというスケールの中で、つくり出されるICの種類はなんと約1,000種以上。
大量生産用ラインの他に複数の生産ラインを組み合わせた複雑な生産体制で「多品種・大量生産」を実現し、さまざまなお客さまの要望にお応えしています。
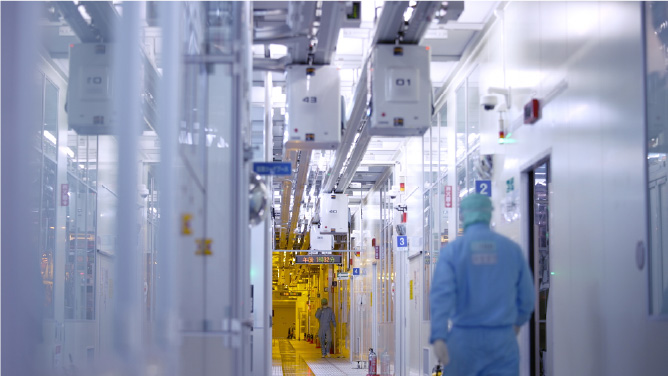
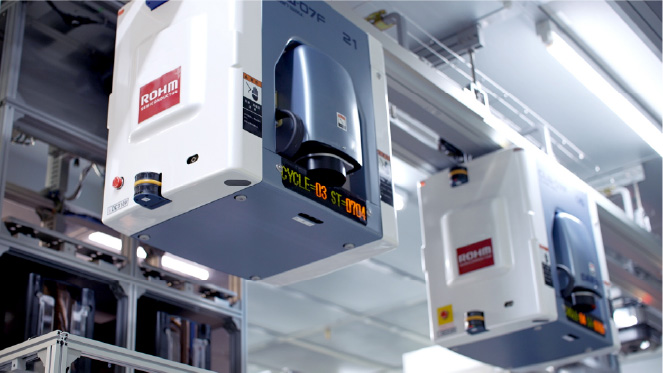
12インチウエハが24枚格納されるポッドが
クリーンルームの頭上を縦横に行き交う。
投入から出荷まで平均25kmの距離を移動する
モビリティ社会の進化とともに
現在、ローム浜松の生産品目の中で生産量が際立っているのが自動車向けの製品です。1999年の設立当時より手掛けてきた分野ですが、少しずつお客さまからの信頼を高め、今ではローム浜松の生産全体の60%を占めるようになっています。
百年に一度の大変革と言われるEV/HEVへの転換、ASV(先進安全自動車)の普及や自動運転の進化をはじめとする電子部品の飛躍的な増加にともない、自動車向け製品のニーズはまだまだ右肩上がりが続くと考えられています。
ただ同時に、車載製品はエンドユーザーの安全性に直接関わってくるため、製品の安全規格や信頼性規格も非常に厳格なものとなります。(例:AEC-Q100・IATF16949・ISO26262など)
これまでに30億個以上のICを自動車関連のお客さまに供給してきたというローム浜松。長年にわたって積み重ねられたこの数字は、徹底した品質管理と厳しい要求に応えてきた証ともいえるでしょう。

ローム浜松における車載製品生産実績
2021年における生産チップ数は約14億個を数える。
2014年から2021年に約7倍の伸びとなっている。
単に要求仕様を満たすだけで自動車への採用が決まるような市場ではないことは言うまでもありません。
どのようにお客さまの信頼を獲得し、今日の生産の主軸と呼べる分野にまで成長させることができたのかを、LSI生産本部第1製造部の山下氏に聞いてみました。
BiCDMOS12インチ(300mm)への挑戦
当時のBiCDMOSプロセスは8インチが世界的に主流でして、我々も8インチラインで生産していました。プロセスノードも0.6μmだったんですが、ローム浜松では既に通常の12インチウエハのラインは稼働していましたし、またCMOS微細化技術も保有していました。
ロームとしてはアナログICでの競争力をさらに高めなければならない、とうことで2006年から、BiCDMOSプロセスの微細化・大口径化・・・つまり12インチ/0.35μmに同時にチャレンジし始めました。当時はその他にもプロセスラインの開発立ち上げが同時進行していて、多くの若いエンジニアと一緒に、まさに24時間体制で開発を進めていました。」
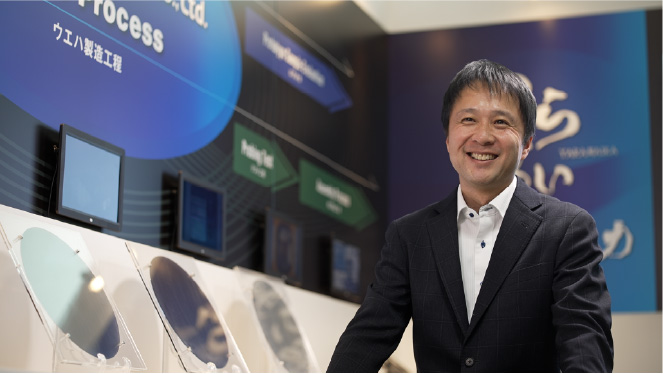
入社するまで「半導体って何?」というレベルだった
「落ちこぼれ」からスタートしたローム浜松での日々。
自身の成長を促してくれた環境に感謝しているという。
昨今の勤務体系では絶対にあり得ない話ですが、と苦笑しながら話してくれた山下氏。
「もう一度やれと言われたら、正直厳しいかもしれませんが」と前置きしながらも、そのチャレンジこそが、ローム浜松BiCDMOSプロセスのすべての起源になっている、という強い確信が伺えました。
革新を支える現場力
グローバルメジャー企業も未だ実現していない「12インチBiCDMOSプロセス」に真っ向から挑むようになった背景には、ロームならではの「強み」がありました。
それは、創業以来、脈々と培ってきた製造装置の自社開発技術です。ローム浜松では、プロセスに最適化させた内製の製造装置に加え、製造装置のメーカー技術者と共にチューニングした購入装置を、バランス良く組み合わせて独自の生産ラインをつくり上げています。
12インチ生産ラインの立ち上げ当時は、そのほとんどが内製装置だったこともあり、チャレンジの糸口を自分達の力で手繰り寄せることができたのではないでしょうか。
LSI生産本部第1製造部設備技術1課 谷口氏に当時を振り返ってもらいました。

大好きなバイクは、ほぼ全ての整備を自分で行っている。
モノを大事にする、そのための工具を大事にする、という
ことが結局、自分を守ってくれているのだ、という感覚を
大切にしている。
谷口
「BiCDMOSのウエハプロセスの中で、非常に重要なのが高温処理ですが、12インチではどうしてもシリコンの歪みが出てしまうという課題がありました。
そこで、熱処理炉の部品設計を見直すことで一般的な高温限界を超えた1,200℃の超高温での処理を実現できました。
装置のことだけでなく、ウエハプロセスそのものを深く理解する技術者の知見が、脈々と受け継がれていたからこそ突破できた壁でしたね。欠陥の場所や原因を即座に見極める<勘所>といいますか・・そういうものは、一朝一夕では手に入らないですから。」
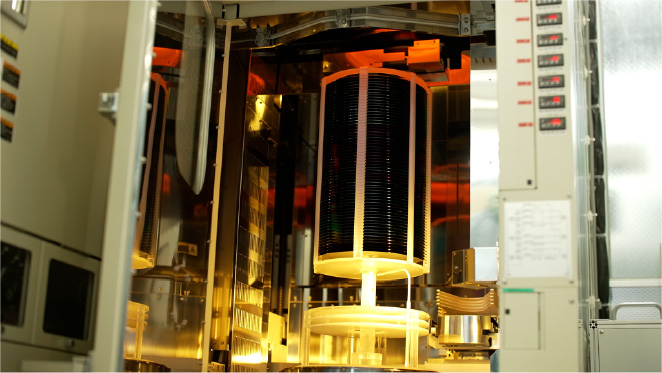
イオン注入されたウエハを、超高温の熱処理炉の中で
成膜処理する工程。製造装置の改善とメンテナンス
がウエハの品質を大きく左右するという。
さらに、ロームの特長でもある垂直統合型生産体制の中、デバイス・プロセス・設備の各セクションが一体となってこの開発プロジェクトに取り組むことができたことも、大きな要因のひとつだと言います。
さまざまな技術的な課題を乗り越えるための「現場力」・・・!
これこそがローム浜松の持つ最大の「強み」と言えるのではないでしょうか。
続いては、それを裏付けるような開発エピソードになります。
フロント・ローディングと品質保証
EV/HEVの主機モータ駆動を担うパワーデバイスを制御する「絶縁ゲートドライバIC」。次世代モビリティの中でも最も重要なデバイスのひとつとして挙げられる製品で、ロームは2016年に世界に先駆けて量産を開始して以来、トップシェアを獲得しています。
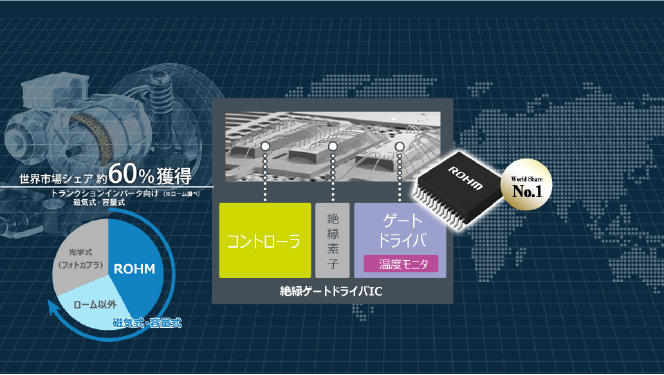
従来フォトカプラ(光学式)が使用されていた絶縁部
に磁気式(マグネティックタイプ)を採用し、
飛躍的な小型化と同時に1パッケージ化を実現
しかし、この全く新しいこの製品の採用に当たっては、お客さまの「信頼」を得るまでに1年以上にわたる苦労があったといいます。当事者であるロームLSI事業本部技術開発担当 和田氏が証言してくれました。
和田
「車載部品の中でも主機モーター駆動の根幹に関わるということもあって、非常に高いレベルのリスクを想定しなければなりませんでした。万が一の故障の際に、エンドユーザーの安全に関わってくることですので<あらゆるリスクを考えたうえでの品質>を担保する必要がありました。」
その一例として挙げられたのが、製造時の異物混入に対するリスクでした。
ローム浜松では、工場設計から始まって、予防保全を含む装置管理、プロセス条件といったあらゆる側面から徹底的に「異物が発生しない」ことを前提にしたものづくりが行われています。さらに欠陥検査機による選別や、製品出荷時のスクリーニングテストによる流出対策も講じていますが、
「もしも異物が混入してしまったらどうなるか?」
「理論通りのスクリーニングが本当に機能するのか?」
を問われるケースがあったということです。
その後の試行錯誤の歩みは、このページ冒頭の動画にてご覧いただくとして、そこで得られた「品質」に対する思いを改めて聞いてみました。
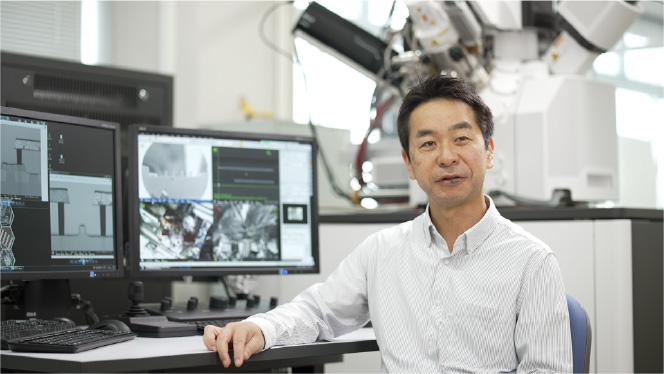
入社時に短期間だったが製造部で仕事をしていた経験から
「その大変さを多少わかっているつもり」と本人の弁。
休日には蕎麦打ちなど「手の込んだ料理」にチャレンジする
という、根っからの「ものづくり」気質!?
和田
「ひとつは、どうやって品質を担保して、お客さまの信頼を得ていくかという面で、非常にいい経験になった、ということです。フロント・ローディングで我々が積み上げている<品質保証>だけでなく、常にその先を考えたリスク管理をしなければならないということ。
もうひとつは、お客さまが感じられる疑問や不安をひとつひとつ解消するための技術や体制。これらをすべて含めて<これが私たちの品質です>と胸を張れるようにしたいですね。」
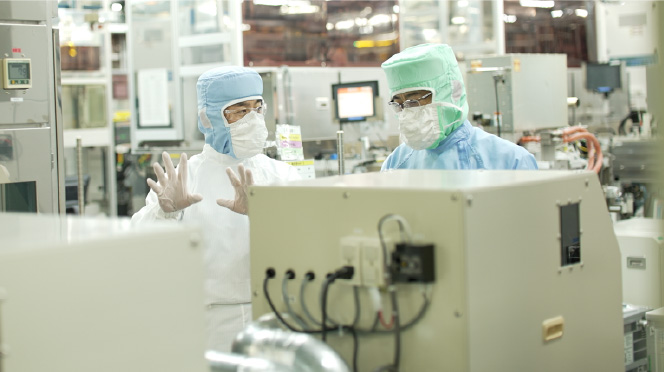
スクリーニングテストの有効性を実証するために、
「意図的」に異物をつくり込んだウエハを数ヶ月かけて製造。
このプロジェクトを通じて、メンバー全員が改めて半導体製造
における社会的責任の重さを改めて共有することができたという。
和田氏は開発セクションとしてローム浜松に常駐し、工程設計やシミュレーション、マスク設計、計測/解析の専門技術者を含めたチームを率いる立場にあります。自らのチームの技術力を高めていくことはもちろん、生産や設備を担う製造セクションとの「密接な関係づくり」にも注力しているとのこと。
和田
「互いの部署がローム浜松の中にあって、物理的な距離が近いということは、我々の持つメリットのひとつです。それに加えて、今でも量産している製品で課題があったら、製造部から相談されることがあって、その際は一緒に考えて取り組んでいます。
そんな心理的な距離感の近さというのも、品質を高めるという面において、実は非常に大切だなと感じています。」
お客さまからの疑問や不安を、開発・製造が一体となって解消していく。このような仕組みは、ロームが採用している垂直統合型体制ならではのメリットに違いありません。しかしそれ以上に、現場がひとつの方向へ向かっていく時に生じる「熱」が、お客さまの「信頼」に繋がることもあるようです。
「品質第一」の、その先へ・・・!
山下
「先日も、あるお客さまが我々の部品の新規採用監査に来られたんですが、その方から『ロームは実直に対応してくれるから』ということを選定理由として挙げてくださったんです。
<お客さまが望むスペックをクリアしている>という返答ではなく、お客さまの元で発生するさまざまな課題に対して、お客さまと一緒になって実直に対応してくれるようなところが、我々の強みではないか、という言葉をいただきました。
私たちが日々やってきた事は、お客さまに届いているんだ!と心から嬉しかったですね。」
その時、山下氏の頭に浮かんだのは、ロームが企業目的として掲げる「品質第一」という言葉でした。それは、単に良い特性のものを供給する/良い商品を大量につくるという意味ではなく、お客さまにとっての満足、そのお客さまの先にいるエンドユーザーの満足へと繋げていくことこそが、我々にとっての「品質第一」だと改めて認識したといいます。

「お客さまから<実直さこそロームの強み>という言葉を
聞いたときは、正直ウルっとしてしまいそうになりました。
すぐに工場のメンバーみんなにも伝えに行きました!」
山下
「工場を操業して20数年になるのですが、ウエハ工場の従業員はどうしてもお客さまとの距離を遠く感じてしまいます。我々は何の目的でものをつくっているんだ?というところに立ち返って、従業員みんなで考える機会というものを設けています。」

ローム浜松で働く従業員は約800名。(※2023年5月現在)
地元遠州地方の方言「やらまいか(やってやろうじゃないか!)」を
体現するチャレンジ精神が「現場力」を生み出している。
ともすれば、毎日のルーティンの中で効率優先や規律遵守に陥ってしまいがちな生産工場の現場において、ものづくりの根源的な意味を見つめ直すことは、決して容易いことではありません。
ひとつひとつの製品から「その先にいる人の満足」をつくり出す集団へ・・・!
その決意は、今日もまた誰かの声に耳を傾けることから始まり、未来へと繋がっていくことでしょう。
次世代半導体がつくり出す世界へ
ローム浜松では現在、12インチラインの拡張工事を進めており、2023年7月から順次稼働をスタートさせ、更なる生産量拡大を実現します。
また、新しい技術としては、更なる大電流化への市場ニーズに応えるため、12インチラインに「厚膜Cu再配線プロセス」の展開を順次進めており、更に「DTI(Deep Trench Isolation)」を搭載した0.13μm BiCDMOSのリリースを計画しています。

厚膜Cu再配線プロセス
DTI (Deep Trench Isolation)
山下
「車載分野は、今まさに技術革新が進んでいる真最中です。
常にその時々のお客さまの求める信頼性と品質を・・・いや、お客さまの求める以上のものを提供することが私たちの使命だと思っています。
私たちの<強み>をしっかりとお客さまの声に結びつけていくことで、次世代半導体が創り出す新しい世界に貢献することができればと思っています!」
関係リンク先
ローム浜松株式会社 https://micro.rohm.com/jp/hamamatsu/
山下
「自動車用の製品に限るわけではないのですが、我々は常に<品質>にこだわったものづくりに挑戦し続けてきた、そんな20数年だったと思います。その中でも大きな原動力になったのが、2009年に世界に先駆けて量産に成功した12インチのBiCDMOSプロセスでした。